By: Zachary Lamas
This article originally appeared in the Summer 2020 issue of BEEKeeping Your First Three Years
Building boxes can be quite profitable and rewarding for small scale beekeepers. If you have a little space, comfort around a table saw, and access to inexpensive lumber, then building bee boxes can be a great supplement to your beekeeping income. In this article I will explain the reasons why I make surplus boxes, and how they assist with the company’s profitability. I will also depict how one person with a few tools and a smart setup can efficiently turn out a lot of equipment. Lastly, there are pictures to help demystify simple joints and the frame shelf for anyone unfamiliar.
Small scale production: simple and quick
When I started expanding my apiaries I could not afford to have as many colonies as I wanted without taking out a loan. The equipment costs were going to be too much. Luckily, I was working as a carpenter, and had the ability to greatly reduce the cost of most of my equipment. Bottom boards, inner covers and covers were low hanging fruits in the potential cost-saving department. At their core they are all just flat surfaces with rails tacked onto them. The boxes themselves aren’t difficult. If you have a great source of lumber, then you’re set to save a lot of money. Here is how I did it.
Sawmills are in a minor quandary when producing graded lumber. Lumber is graded, by the quality of the grain and knot sizes. The higher the grade, the higher the price fetched per board foot. A long board may fetch a low price per board foot because of some gnarly knots. However, if these knots Fall on the ends, then they can be cut off, and the shorter, knot free board can fetch a lot more money. This is simplified, but characterizes the quandary mills get themselves into. They produce and accumulate a lot of short, knotty lumber during their milling. These short pieces are often bundled onto pallets, and offered for sale at a great discount. I’ve been able to get boards to make quality bee boxes for as little as 16 cents a board foot. With approximately 6 linear board feet in a bee box, you can see we can make boxes at a discount.
Making boxes isn’t just a cost cutting method. They are a great resource to improve your beekeeping and to increase sales. I make surplus boxes during the Winter months when I have free time to work in the shop, and I make more than I think I will need. If the season is great, I am guaranteed to have extra equipment on hand. I focus on making good decisions on my beekeeping, and not a limited resource e.g. boxes I don’t have. The extra equipment is great to sell. Hobbyist beekeepers are not incentivized to stockpile extra equipment, which means a small sideliner can have easy Spring and Summer sales as local beekeepers need boxes on the fly. (I actually just leave boxes on my front porch, and request patrons toss money through my mail-slot. It saves me a lot of time not manning a store, and works with other’s schedules).
Passively selling extra boxes makes great investment sense. With my markup, I need to sell less than 20 boxes out of 100 to pay for all the lumber. With those few sales, I recoup my initial expenses, and all the extra boxes, including the ones I am putting on my colonies are paid for. I highly suggest this for retired beekeepers who are bringing in a side income or small scale sideliners. We can increase profitability without losing track of our primary focus: keeping productive, healthy bees.
Case Study: A weekend with dad
My dad is pretty handy, and wants to supplement his income when he retires. He likes bees, and sees a small bee store as a possibility while selling nucleus colonies. He isn’t looking to replace his income, but rather supplement his retirement. He is comfortable working with power tools, and enjoys working outside. Making his own boxes means he has an inexpensive supply of his own beekeeping equipment, as well as inventory to sell from time to time.
We took the opportunity after Christmas to build boxes. We started with a truck load of lumber, and finished with unassembled boxes. Day one was easy and took about 2.5 hours. I drove to the lumber yard, and bought l, 150 board feet of off grade lumber for 40 cents a board foot. These were all 12 inch widths of ¾ lumber that ranged from 6 to 16 feet long. Once strapped, I drove home. Day 2 was the “break down day”. On this day boards are cut into the sides or ends of a bee box with one saw, and then “ripped” to width on another saw. Each saw is setup once. That old adage, measure twice and cut once? Well, we measure twice and cut a few hundred times. Day 3 the ends receive a rabbit joint and the frame rest. Both cuts are made with a “dado blade”, which is pictured below. At this point our boxes are considered “unassembled” and can either be stapled together or stored flatly in a dry area.
Day One: Picking up the Lumber
We source the lumber for our bee boxes directly from mills. The markup at hardware shops and box stores is prohibitively expensive. The same quality lumber can be purchased by calling around to your local mills. Some mills do not retail at all, while others do. You’ll have to call around to find out. You’ll want to know if the lumber is planed, and kiln dried. Planed means the lumber has shaved down to final dimensions. The surface and edges will be smooth. Kiln dried means the lumber had been placed into a special shed to remove most of the moisture from the wood. Be careful with using air dried lumber for bee hive boxes.
Most mills sell planer outs or shorts. Either are lingo for off grade lumber that can be purchased at a steep discount. We don’t need perfect long boards to make beehive boxes. With practice you can learn to cut around the knots in off grade lumber. In my opinion, it is often worth the slight extra work. When you contact the mill, ask if they sell off grade lumber, shorts or bundles of end cuts or planer outs. Each mill is different.
Day one overview:
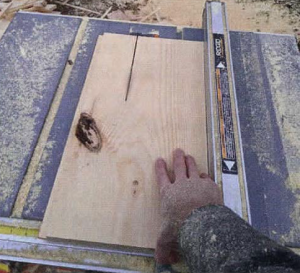
Here we have a piece that has already been trimmed to 19¼”. I am now “ripping” the piece to height on the table saw. The portion of the board to the right of the saw will be my bee box. The portion to the left will be scrap. Notice by cutting it this way my final product will not include this nasty knot.
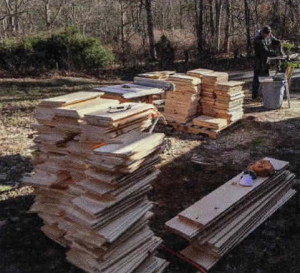
Our worksite in action. Dad is making one cut on the chop saw. I am making another on the table saw. You don’t need a state of the art shop to make quality bee boxes. Keep ergonomics and safety in mind and you can efficiently make boxes from a simple setup.
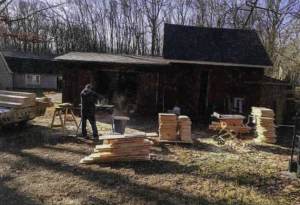
Dad grabs a board right from the truck. The saw has already been set so he doesn’t use his tape measure anymore. He squares the end and then begins cutting. He moved a trash can to his right .. To limit bending, he just sets his cut pieces there until he finishes a board. Then he walks the Jew pieces over to the stacks on the pallets. I trim the pieces on the table saw. The defective boards are very knotty or have visible splits in them. They will be used to make bottom boards later on.
Day Two: Setting Up
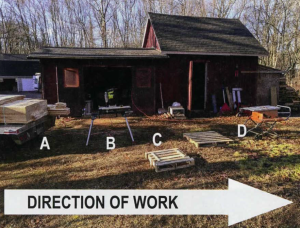
Setup: I really like to work in one direction. This prevents unneeded stepping throughout the day. I set the first saw right near the load of lumber. Boards move from the truck directly to the chop saw. The person on the chop saw makes one repetitive cut over and over, placing the cut pieces of wood occasionally on the pallet marked C. The person at Station D. is making a different cut on the piece of wood already cut from person B. We tum out boxes quickly because the saws are set only once, and the same cut is performed repeatedly. We calmly, steadily work in one direction from A to D.
A friend once said 5 minutes of setup is worth an hour of work. He couldn’t have been more correct! You do not need a fancy shop or the best tools on the market to enjoy making beehive boxes. A little thought into the setup goes a long way. We are doing a repetitive task, often for several hours without stopping. Our setup should be safe and ergonomic foremost. This means properly stationed tools, walkways and standing areas are free of trip hazards. A poor setup means you’ll be repetitively bending in ways that will hurt your shoulders and back. We want to limit reaching over or lifting items while extended. Our wood scrap should not land around our feet either. They accumulate quickly, and become pesky as we work.
If you have indoor space then your setup will have to include a proper dust collection system. This is a must and there is no way around it. Cutting lumber creates visible and invisible dust particles. They are hazardous to your health. We worked outside and wore dust masks.
Day 2: First Cuts-Measure twice, Check once, Cut a few hundred times.
Cutting to Length
We want to make our boxes quickly. We do that by only setting our saws once a day. Afterwards we just make the same cut over and over again. On the first day we are making two almost identical pieces. The sides of our box will be 9 5/8 inch high, 19 1/8 long. Our ends will be 9 5/8 high and 16 ¼ long. Each piece is ¾ of an inch thick, and the ends are square, straight cuts. To get the lengths, we are making one repeated cut over and over again. There is no need to use a tape measure each time we need to make the same cut. Instead, we will set the distance of the saw blade to a “stop” at the exact length of our desired cut. We slide our board to the stop, and then make the cut. If that piece measures correctly, then we begin cutting the many pieces we will need. Make sure to first square up the end of your board first!
Cutting to Height
Now that our pieces are cut to length, we will want to cut them down to the final 9 5/8 height of a deep box. I am fortunate that my lumber supplier sells edged lumber with little wane in the board. I do not edge my boxes ahead of time. If your lumber has a lot of “crown”, you may need to trim this or edge it. As a friendly public service announcement- it probably doesn’t matter much.
I use a table saw to cut my boxes to height. Set the saw to 9 5/8 and pass a piece of scrap wood through. Measure and if this works, then start passing your pieces through. You’ll want to cut the worst knots out during this phase. Sometimes a piece will have a horrible knot that can be completely cut out by turning it into a 6 5/8 medium box instead of a deep. This is a great way to use otherwise unsalvageable wood.
Be good to yourself while using a table saw, and follow good practices. We are making one repeated cut over and over again. Take breaks to break up the rhythm. Never force a board through the blade. Importantly, be willing to toss a piece of wood if the pitch pockets or knots make cutting too difficult. These pieces tend to kick back wildly, and you should never feel like you are forcing anything through the saw. If you find yourself doing this, stop, abort mission. Check your setup. Your fence may have come out of square or the blade is now dull. Some boards hold a lot of tension in the grain of the wood. This is caused by how the tree grew. I find flipping those boards and cutting from the opposite side is a quick fix. If it still fills tenuous, then consider passing on that particular piece.
Day Two: Making joints and the frame shelf
The sides of our boxes were completed on day one. On day two we will focus on making the rabbit joint and the frame shelf for our ends. This is super simple. It does require you to have a dado blade and a table saw setup for one. This includes a zero clearance insert and a wooden guard on your fence. *Note: In these photos I do not have a zero clearance insert and the wooden guard is held on by clamps. Don’t do this.
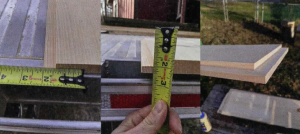
From left to right: We need to make 3 cuts with our dado blade. One on each side, and one on the top for our frame shelf The frame shelf is ¾” high, and ¾” deep. Pictures one and two. The sides that make the rabbit joints are also ¾” deep, but they are ¾” wide.
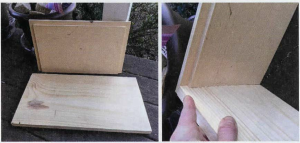
At the end of day 2 this is what we have. The top is our box end with frame shelf and rabbet joint. The bottom is our box side. They fit together as seen in the photo to the right. This makes our rabbet joint. These simple boxes are easy to make, and are durable for all beekeeping operations.
Safety/Hands
We don’t have to work fast, just steady. It is repetitive work with fast moving sharp slow moving, soft things, i.e. saw blades and fingers. So there is never any rushing. If a saw gets out of square, we stop. If a particular board is difficult to cut from excessive knots, we don’t cut it. If we get tired, stop. Take a break. Power tools can be used daily and safely, but much of that comes from your own decisions. Make those decisions each day, and moments within the day. Fingers are expensive, not replaceable. Always wear ear and eye protection along with dust protection.
Cutting around defects
Ignore the defect. There is a perfect beehive box to the left and to the right of this nasty break in the board. Notice how there are no knots, and a great smooth grain on each side. These bee boxes will be beautiful and strong. By cutting around this defect, we end up with select grade boxes. What little waste becomes kindling.
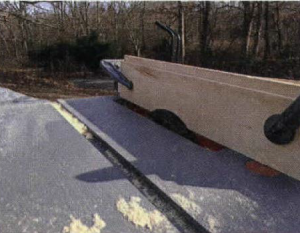
A dado blade is a stack of special blades that removes a notch of wood, unlike a normal blade that cuts through a board. This is pictured on the left. The blades are spinning. Only the exposed blades not under the wooden guard will cut our frame shelf and rabbet joints. Note: The homemade clamped guard is not advised. My mom took over and made all the rabbet joints and frame shelfs. It is very easy, repeatable work. We made 120 unassembled deep boxes in a short time.